Processing Low Grade Iron Ore And Fines
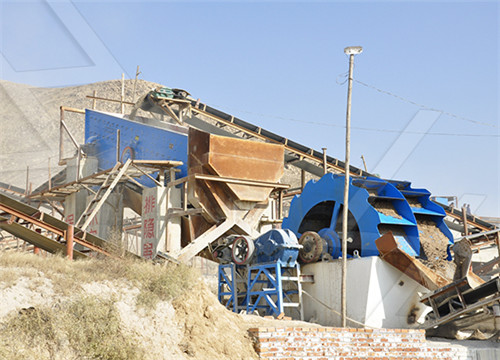
Beneficiation of Clay-Rich High-LOI Low-Grade Iron Ore
2022年6月4日 The unutilized iron ore fines (IOF, − 10 mm, 45% to < 60% Fe(T)) left at various mine sites during blasting and processing are rich in goethetic-hematite associated with high clay and considered a potential iron ore resource. The variation of loss on

Evaluation of Dry Processing Technologies for Treating
2020年10月25日 Nunna et al. (2020) processed low-grade hematite-goethite iron ore fines containing 54.5 wt% Fe, 2.10 wt% SiO 2, and 7.97 wt% Al 2 O 3 with an air classifier to
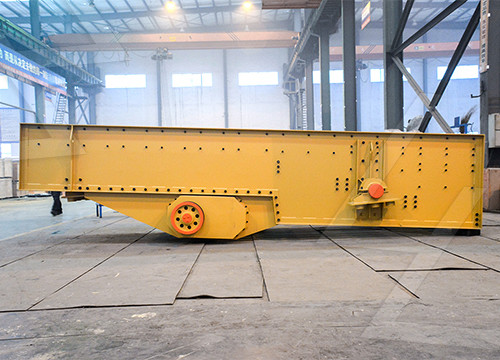
Mineralogical Study of Low and Lean Grade Iron Ore Fines
2022年8月9日 The present study focuses on the mineralogical aspects and roasting of iron ore (Fe: 55.4%) fines in both fixed bed and fluidized bed roaster. Goethite is the

(PDF) Strategies for processing low-grade iron ore
2009年9月23日 The unutilized iron ore fines (IOF, − 10 mm, 45% to < 60% Fe(T)) left at various mine sites during blasting and processing are rich in goethetic-hematite

Iron Ore Recovery from Low Grade by using Advance
2015年1月1日 Abstract. With increasing global demand of iron ores due to the huge requirement of steel all over the world, important iron ore producing countries have

Non-isothermal reduction kinetics of low-grade iron ore
The low-grade iron ore and coal were both ground to 80 % of it could be screened through 0.074 mm sieve for pelletizing. Then, the mini-pellets were obtained by pelletizing the

Iron Ore Pelletizing Process: An Overview
2018年7月11日 The iron ore production has significantly expanded in recent years, owing to increasing steel demands in developing countries. However, the content of iron in ore deposits has deteriorated and low

Processing of Goethitic Iron Ore Fines SpringerLink
2015年5月9日 Goethitic iron ore is present in hydroxide form and leads to disintegration of pellets during firing process. Hence, it is in this direction an attempt has been made to

(PDF) Processing of Low Grade Iron Ore Fines
2014年12月1日 On an average, about 400 Kg of solid byproducts (i.e. wastes) are generated in the iron and steel plant per tonne of crude steel production. The World Steel Industry had produced about 1620.9 Mt

(PDF) Effective Beneficiation of Low Grade Iron
2008年1月1日 Optimum iron ore recovery of 78.6% was achieved with 63.7% Fe in concentrate when the jig was operated at medium stroke, with an average water velocity and at a particle size of below 5 mm. The
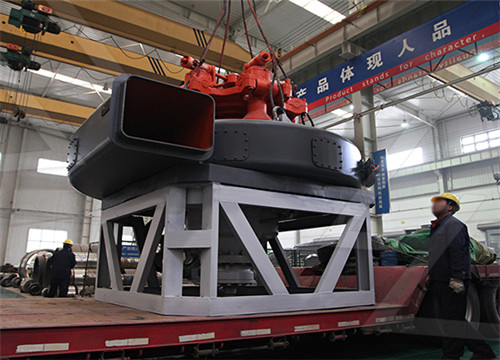
Evaluation of Dry Processing Technologies for Treating
2020年10月25日 Nunna et al. (2020) processed low-grade hematite-goethite iron ore fines containing 54.5 wt% Fe, 2.10 wt% SiO 2, and 7.97 wt% Al 2 O 3 with an air classifier to remove −20 μm fines, followed by
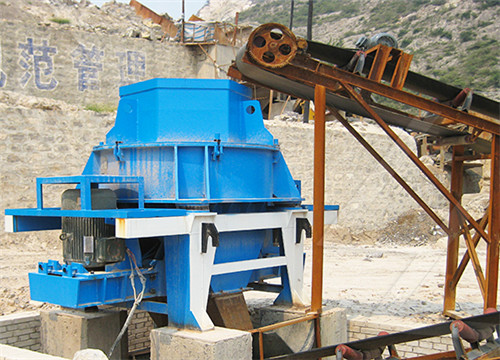
Metals Free Full-Text Impact of Iron Ore Pre-Reduction
The process eliminates the prior agglomeration process, and iron ore fines can be directly introduced. The process is compared with fluidized bed reduction, which uses hydrogen as a reducing agent and fine ore as feed material. The results provide evidence indicating the advantage of using hydrogen plasma reduction to process low-grade iron

Non-isothermal reduction kinetics of low-grade iron ore
The low-grade iron ore and coal were both ground to 80 % of it could be screened through 0.074 mm sieve for pelletizing. Then, the mini-pellets were obtained by pelletizing the row materials with sodium additive in a disc pelletizer. The mass ratio of iron ore, coal fines and sodium additive are 1000: 169: 49.
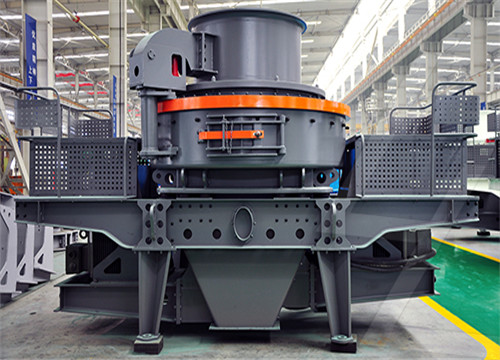
Circored Fine Ore Direct Reduction Plus DRI Smelting:
2022年2月10日 The large furnace volume enables the processing of low-grade iron ore with high gangue content and thus the use of BF-grade feed for DRI production. Keywords. Iron and steel; Environmental effects the growing demand for a direct reduction process utilizing iron ore fines directly to decrease HBI production cost by avoiding a costly
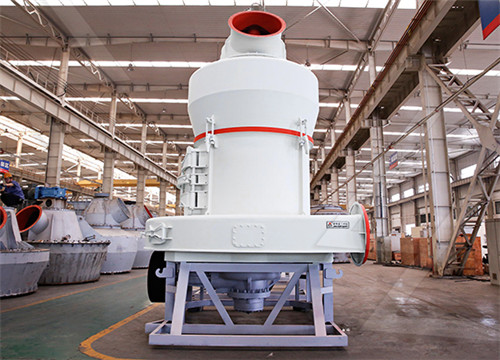
Beneficiation of Low-grade Iron Ore Fines by Using a
2019年7月17日 ABSTRACT The current beneficiation study examines the potential for separating ultrafine low-grade iron ore materials using a circulating-type air classifier. Statistical analysis using Response Surface Methodology (RSM) was implemented for optimization of the separator critical processing parameters to achieve sharp separation
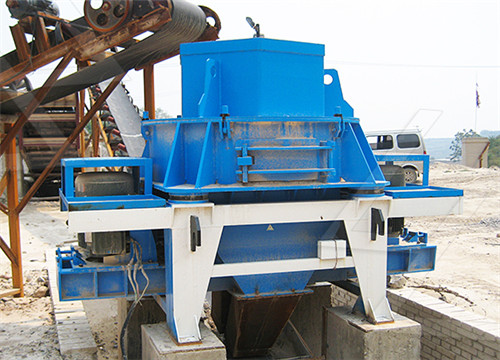
Sustainability Free Full-Text Preparation of Red Iron by
Limonite is a representative low-grade iron ore due to its complex mineral and elemental composition. In this , the union process was employed to separate the iron elements in low-grade limonite. Firstly, a rough iron concentrate was obtained under 1.0 T of magnetic field intensity and −0.074 mm > 94.84% of grinding fineness; then, the

ITmk3 ® Process|KOBELCO Kobe Steel,. Ltd.
At the present, low-grade iron ore is processed into iron ore fines, high-grade iron ore concentrate and pellets through grinding, beneficiation and firing, and is fed into the blast furnace and DR plant. In the ITmk3 ® Process, iron ore concentrate and non-coking coal are mixed together and agglomerated into green pellets. These pellets, fed

BENEFICIATION OF LOW/OFF GRADE IRON ORE: A REVIEW
2020年8月1日 The prominence is to develop a method for the beneficiation of low grade/slimes/fines iron ore which should be cost effective. It is also very necessary that beneficiated ore should be suitable for sinter, blast furnacein pellet making. Pan, S P, Parsad, N and Mishra, B. K, (2001) “Characterization and processing of iron ore fines of

Efficient Utilization of Siderite- and Hematite-Mixed Ore
Steel is an important industrial raw material and plays an important role in industrial construction. Studying the efficient utilization of complex refractory iron ore with large reserves is of great significance to ensure the strategic safety of China’s iron and steel industry. Focusing on the typical mixed iron ore of siderite (FeCO3) and hematite

Influence of sinter basicity (CaO/SiO2) on low and high
2014年5月28日 Abstract Iron ore sinter, constituting a major proportion of blast furnace burden, significantly impacts the blast furnace performance. The chemical composition of iron ore fines, particularly alumina, sinter basicity and sinter MgO together with the thermal conditions that sinter blends are subjected to play an important role in the formation of

Metals Free Full-Text Impact of Iron Ore Pre-Reduction
The process eliminates the prior agglomeration process, and iron ore fines can be directly introduced. The process is compared with fluidized bed reduction, which uses hydrogen as a reducing agent and fine ore as feed material. The results provide evidence indicating the advantage of using hydrogen plasma reduction to process low-grade iron
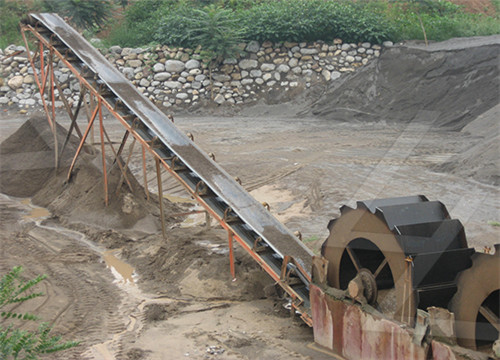
Experimental study on the beneficiation of low-grade iron
2014年8月17日 AbstractBeneficiation of −2 mm low-grade iron ore tailings (507%Fe, 108%SiO2 and 44%Al2O3) from Western Australia was studied. Experimental study on the beneficiation of low-grade iron ore fines using hydrocyclone desliming, reduction roasting and magnetic separation with lesser kaolinite and shale. Two processing options were

Beneficiation Strategies for Removal of Silica and Alumina
2021年11月24日 The major concentration methods that may be applied to upgrade lower-grade lump iron ores include magnetic separation, wet and dry heavy media separation, and air-pulsed jigging. The technologies applicable to beneficiating iron ore fines include wet and dry gravity and magnetic separation, flotation, and roasting followed by magnetic

Non-isothermal reduction kinetics of low-grade iron ore
The low-grade iron ore and coal were both ground to 80 % of it could be screened through 0.074 mm sieve for pelletizing. Then, the mini-pellets were obtained by pelletizing the row materials with sodium additive in a disc pelletizer. The mass ratio of iron ore, coal fines and sodium additive are 1000: 169: 49.
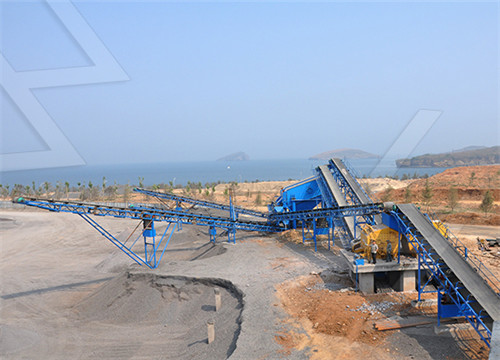
Sustainability Free Full-Text Preparation of Red Iron by
Limonite is a representative low-grade iron ore due to its complex mineral and elemental composition. In this , the union process was employed to separate the iron elements in low-grade limonite. Firstly, a rough iron concentrate was obtained under 1.0 T of magnetic field intensity and −0.074 mm > 94.84% of grinding fineness; then, the
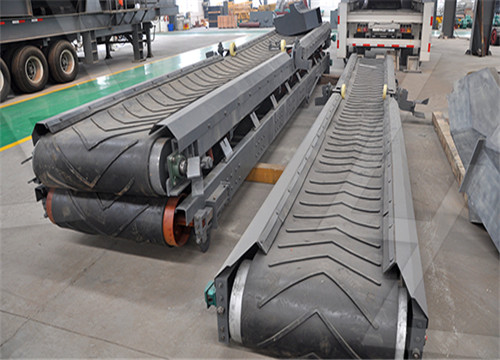
Efficient Utilization of Siderite- and Hematite-Mixed Ore
Steel is an important industrial raw material and plays an important role in industrial construction. Studying the efficient utilization of complex refractory iron ore with large reserves is of great significance to ensure the strategic safety of China’s iron and steel industry. Focusing on the typical mixed iron ore of siderite (FeCO3) and hematite
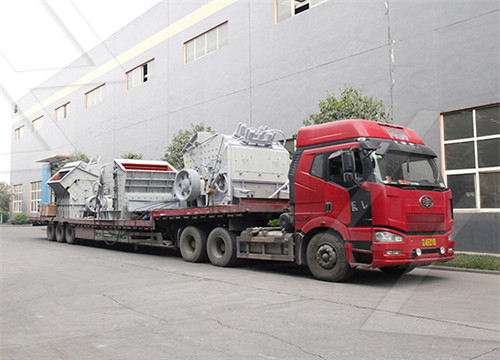
Iron Ore Processing
2017年11月17日 Key words : L ow grade iron ore, beneficiation, gravity, magnetic, sinter, pellet . 1. Introduction India is one of the leading producers and exporters of ir on ore in the world with over 28 billion tonnes of iron ore reserves [1]. P rocessing of low grade iron ore is inevitable as a r esult of increase in production and consumption of high
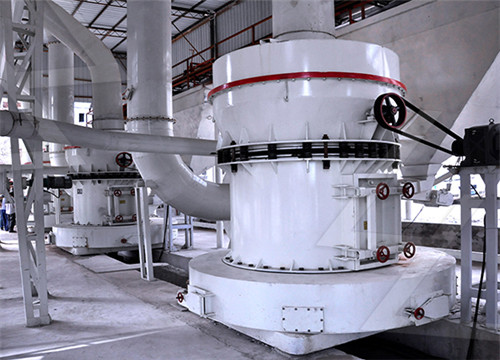
Influence of sinter basicity (CaO/SiO2) on low and high
2014年5月28日 Abstract Iron ore sinter, constituting a major proportion of blast furnace burden, significantly impacts the blast furnace performance. The chemical composition of iron ore fines, particularly alumina, sinter basicity and sinter MgO together with the thermal conditions that sinter blends are subjected to play an important role in the formation of

BENEFICIATION OF LOW GRADE IRON ORE FINES BY
ABSTRACT The effectiveness of jigging operation for the beneficiation of low-grade iron ore deposits of Orissa, India has been investigated. Iron ore sample obtained from Barbil region of Orissa containing very high amount of silica and alumina was crushed using the laboratory jaw crusher and roll crusher to prepare different particle sizes.

A Study on Removal of Clay Minerals from Barbil Region
Spectroscopic analysis revealed that iron ore samples obtained from the Barbil region of Odisha contain a high amount of silica and alumina in the form of clay minerals (e.g., kaolinite) contributed as a loss on ignition (LOI) in the iron-making process. Iron ore fines of below 10 mm size were subjected to a laboratory-scale screw scrubber, and