Electrode Wear Excessive
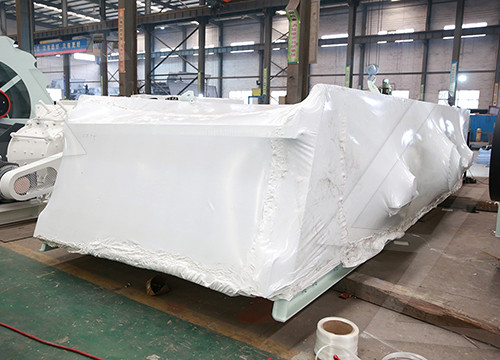
Research of lower tool electrode wear in simultaneous
2014年8月1日 Using deionized water as a dielectric fluid, tool electrode wear can be lowered but excessive electrolytic-erosion occurs, which causes low-shape accuracy and damages the surface of the workpiece. In order to lower electrode wear, and at the same

The Effect of Graphite-Powder-Mixed Kerosene on Tool
2021年9月6日 Electrical discharge machining (EDM) is a useful method for processing shapes on any conductive material. In particular, this machining method can be applied

Electrode Wear an overview ScienceDirect Topics
The Excimer Laser. David J. Elliott, in Ultraviolet Laser Technology and Applications, 1995 3.8.3 Laser Electrodes. Laser electrode wear will also cause a degradation of laser
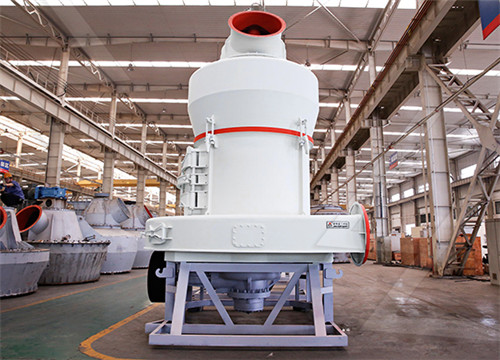
Keys to Controlling Electrode Wear MoldMaking
2002年6月1日 Excessive electrode wear will make it harder to keep the gap clear for efficient cutting and to make an accurate cavity. Although thin rib electrodes are
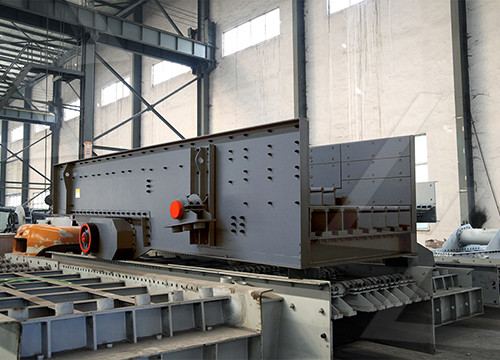
Six reasons consumables wear too soon Hypertherm
2016年3月10日 Changing out consumables too soon is a common cause of excessive consumable use. Many businesses change consumables after a set number of pierces or
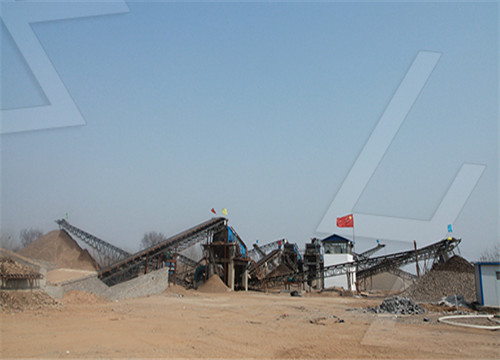
5 Common Welding Defects, and How To Prevent Them
2021年11月23日 Some of the more common ones are listed below. 1. Electrode Wear. Deformation of electrode tips can occur over time as a result of use, but if the wear

Reducing electrode wear in EAF steelmaking [2022] Luxmet
2022年1月19日 Or if the electrode is clamped at the electrode joint it may break due to excessive stress applied to the joint. How to reduce electrode wear. The graphite

How can I minimise electrode wear in resistance spot
The electrode diameter should be a minimum of 2.5 to 3 times the tip diameter to increase the effectiveness of cooling. The cooling tube should be cut at 45° and directed on the
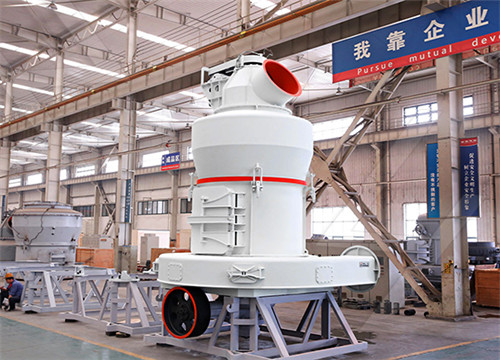
Drilling Small, Deep Holes with Precision EDM
2013年11月1日 However, in lab testing, GF AgieCharmilles accomplished the same task on its new Drill 300B, a three-axis high-speed EDM drilling system with IPG Generator

Electroformed electrode with excessive corner wear.
Download scientific diagram Electroformed electrode with excessive corner wear. from publication: Electroforming of rapid prototyping mandrels for electro-discharge machining
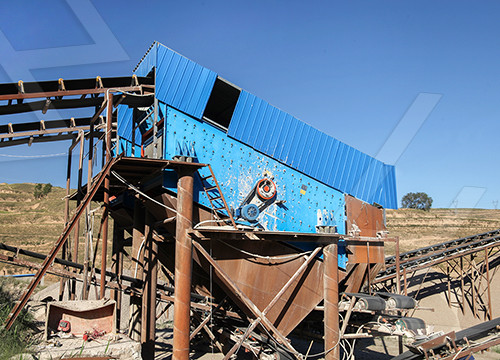
The analysis of EDM electrodes wear in corners and edges
2020年10月17日 The wear of the electrode does not only mean its loss but also the degradation of the shapes that are transferred to the resulting workpiece. For this reason, a design of experiments was conducted with 6 input factors, 2 were categorical: the electrode material (copper, graphite) and workpiece material (steel 1.2363 and steel 1.2343ESR)
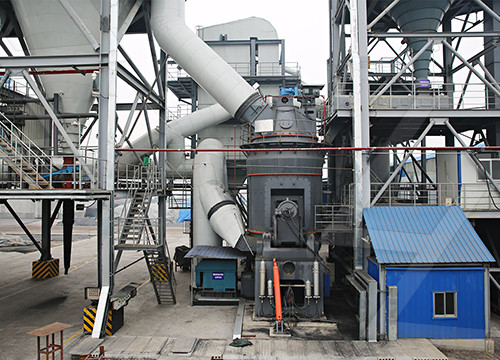
Machine-vision-based electrode wear analysis for closed
2021年11月25日 The purpose of this study was to develop a closed-loop machine vision system for wire electrical discharge machining (EDM) process control. Excessive wire wear leading to wire breakage is the primary cause of wire EDM process failures. Such process interruptions are undesirable because they affect cost efficiency, surface quality, and
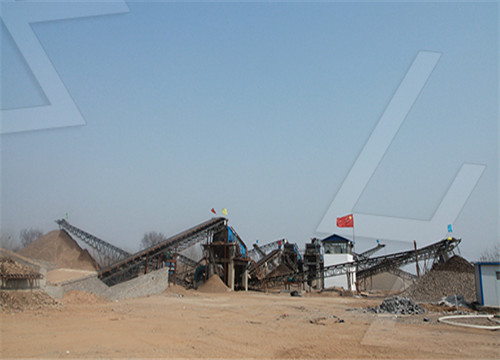
Materials used for sinking EDM electrodes: a review
2018年12月7日 The electrode wear of AF5 electrode was much smaller than the electrode wear of EDM3, although both electrodes had a low tool wear. Also, excessive electrode wear was reported, with the porosity of the electrodes the main cause of it. As shown in the related work, there are many variations of producing EDM electrodes by AM and each
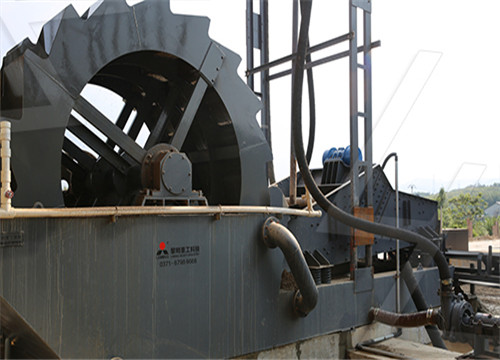
Research of lower tool electrode wear in simultaneous
2014年8月1日 For reducing the electrode wear and suppress excessive electrolytic-erosion, Yin et al. (2014) studied the mechanism of exploiting electro-deposition to compensate electrode wear in simultaneous
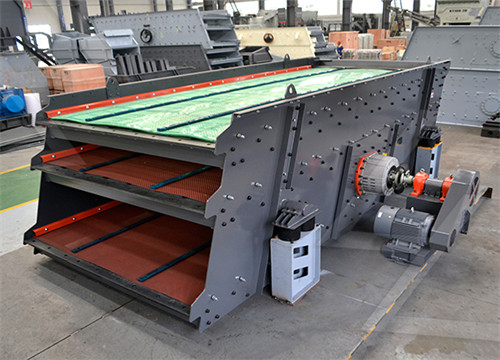
Influence of Wear Pattern of Graphite Electrode on EDM
2020年1月1日 Using oil-based working fluids, graphite electrodes have different wear and deposition patterns under different conditions. This study aims to control the final geometric accuracy of deep and narrow slot machining by optimizing electrical parameters. Experiments using orthogonal design were conducted with a 20×1×20mm narrow slot.
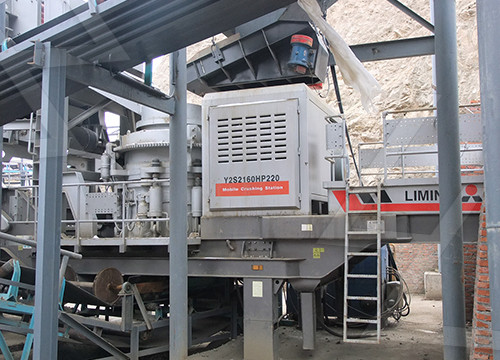
Uncertainty of the electrode wear on-machine
2021年4月1日 The experiments were performed on a Sarix SX-200 micro EDM milling machine equipped with a wire EDM grinding device and a Laser scan micrometer Mitutoyo LSM-500 s (Fig. 1).Blind holes were machined where the electrode was performing circular motion in x-y plane. The tungsten carbide tool electrode with 300 μm in diameter was
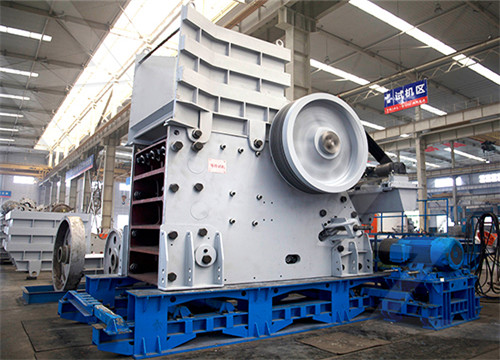
Reducing electrode wear in EAF steelmaking [2022] Luxmet
2022年1月19日 Or if the electrode is clamped at the electrode joint it may break due to excessive stress applied to the joint. How to reduce electrode wear. The graphite electrode consumption is a large part of the cost of steel production in the EAF process route, but this cost can be decreased with optimized EAF process practices.
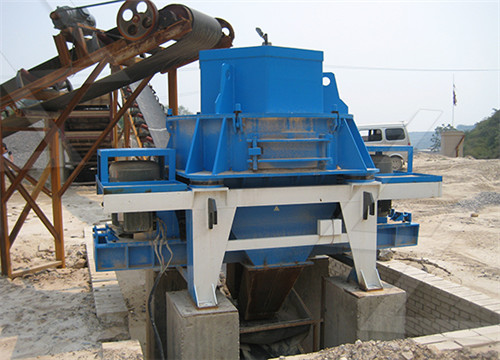
Materials Free Full-Text Comparison of Properties of
2020年11月29日 In this article, the results of research on the metal-mineral-type abrasive wear of a wear-resistant plate made by a tubular electrode with a metallic core and an innovative chemical composition using the manual metal arc hardfacing process were presented. The properties of the new layer were compared to the results of eleven wear

Five reasons to use graphite EDM electrodes
2017年6月27日 EDM operators know that excessive wear results in the use of extra electrodes or frequent redressing. Graphite is able to achieve electrode wear of less than 1% in relation to the depth of cut, while working to more aggressive machine parameters. This means, unlike copper, the high amperage and longer on-times actually preserve the

Electroformed electrode with excessive corner wear.
Download scientific diagram Electroformed electrode with excessive corner wear. from publication: Electroforming of rapid prototyping mandrels for electro-discharge machining electrodes The
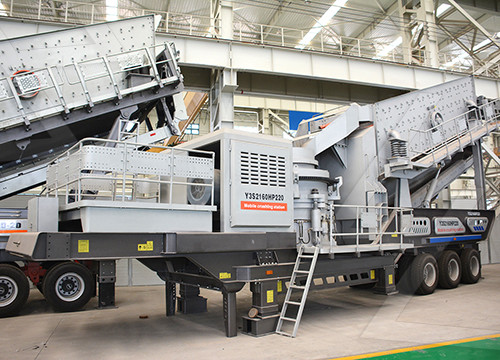
Processes Free Full-Text General Approach for
2021年4月13日 Electrodes for resistance spot welding inevitably wear out. In order to extend their service life, the tip-dressing process restores their original geometry. So far, however, the point in time for tip-dressing is

Machine-vision-based electrode wear analysis for closed
Abstract: The purpose of this study was to develop a closed-loop machine vision system for wire electrical discharge machining (EDM) process control. Excessive wire wear leading to wire breakage is the primary cause of wire EDM process failures. Such process interruptions are undesirable because they affect cost efficiency, surface quality, and process
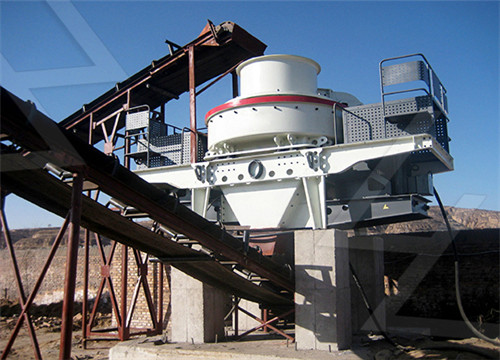
Machine-vision-based electrode wear analysis for closed
2021年11月25日 The purpose of this study was to develop a closed-loop machine vision system for wire electrical discharge machining (EDM) process control. Excessive wire wear leading to wire breakage is the primary cause of wire EDM process failures. Such process interruptions are undesirable because they affect cost efficiency, surface quality, and

Materials, Devices, and Systems of On‐Skin Electrodes for
2020年12月4日 The accuracy of this HMI device reached 92 ± 2%. EOG signals acquired with soft-fractal electrodes were also utilized for wireless wheelchair control by Mishra et al. Similar to the above method, the subject was required to wear vertical and horizontal electrodes on the corners of the eyes. Likewise, the real-time EOG datum were wirelessly
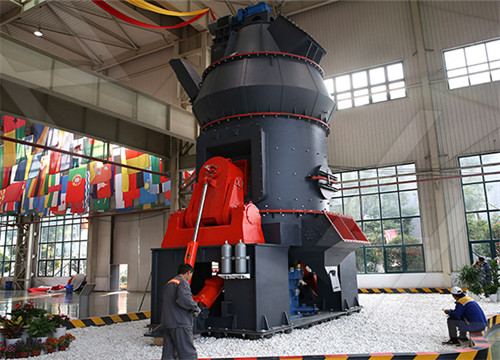
Materials Free Full-Text Comparison of Properties of
2020年11月29日 In this article, the results of research on the metal-mineral-type abrasive wear of a wear-resistant plate made by a tubular electrode with a metallic core and an innovative chemical composition using the manual metal arc hardfacing process were presented. The properties of the new layer were compared to the results of eleven wear
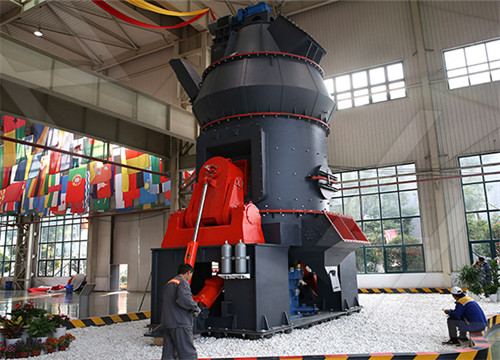
Durability Study of Embroidery Electrode Made of
2022年7月27日 As an important part of intelligent textiles, ECG monitoring clothing has been developing rapidly in recent years with the requirements of flexible, comfortable and reusable real-time monitoring [].Electrodes are the core component of ECG monitoring clothing [].The wet electrode (Ag/AgCl electrode) is the most commonly used in ECG
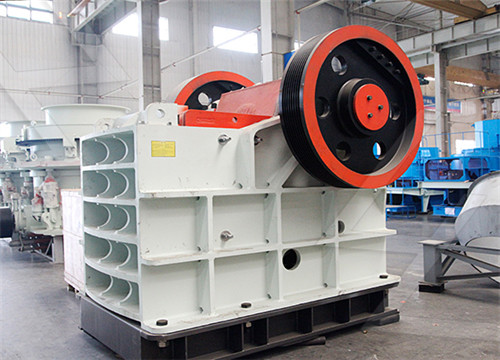
How to Recognize Damaged Plasma Torch
2023年3月9日 The safety zone for emitter wear depth is approximately 0.040” (1.02mm) for copper electrodes and 0.1” (2.54mm) for silver electrodes. Always inspect O-rings for possible damage such as nicks,
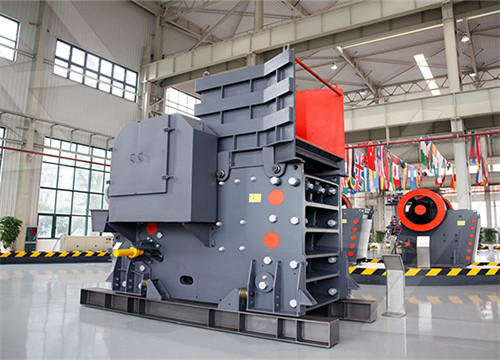
Blue Transparent OLEDs with High Stability and
2023年3月9日 The EEG and reference electrodes were inserted into the skull at ML:2, AP:−2 mm; and ML:−2, AP:−5 mm from the bregma, respectively. The EMG electrode was inserted using a 26-gauge needle and a very thin wire across the trapezius at the back of the neck and tied so that the movement of the trapezius can be received as an electrical signal.
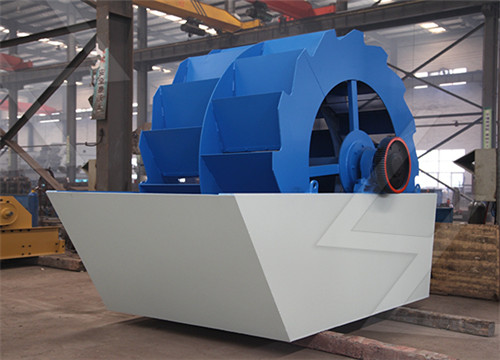
Optimization of Titanium Grade-5 (Ti6Al4V) Alloy on Die
2023年2月24日 Request PDF Optimization of Titanium Grade-5 (Ti6Al4V) Alloy on Die Sinking EDM by Using Copper Tungsten Electrode Die sinking EDM of Ti6Al4V has been carried out with copper tungsten electrode.
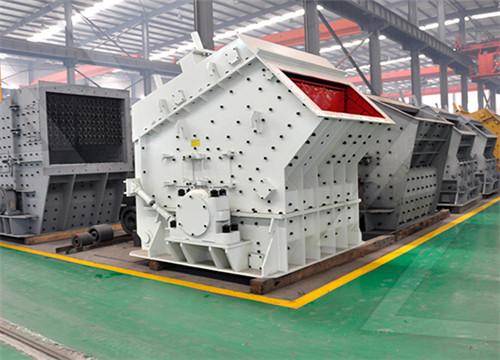
Polyurethane coatings modified by OH-PDMS for anti
2.4.Characterizations of the SiPU-X 2.4.1.FT-IR. The chemical structure of the coatings was characterized by Fourier transform infrared spectroscopy (Thermo fisher Nicolet 6700, USA), and the spectra were recorded 500–4000 cm −1.Test sample preparation method: SiPU-X coating was gently scraped off with a knife and mixed and ground with KBr powder and