Various Iron Ore Processing Activities
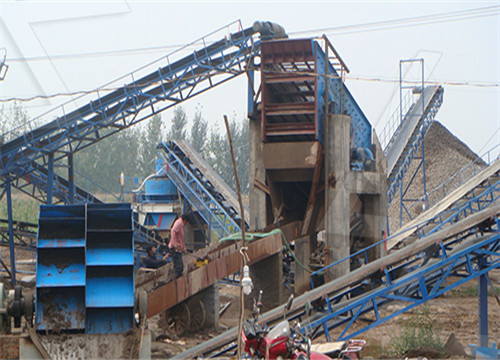
Iron processing Definition, History, Steps, Uses,
iron processing, use of a smelting process to turn the ore into a form from which products can be fashioned. Included in this article also is a discussion of the mining of iron and of its preparation for smelting. Iron (Fe) is a

Full article: Iron ore processing TaylorFrancis
2016年8月24日 This special issue of Mineral Processing and Extractive Metallurgy presents a selection of the best metallurgy limestonedelivered at the very successful

Iron Ore Processing an overview ScienceDirect Topics
In India, where iron ore processing is one of the major industries, the generation of tailings is estimated to be 10-25 % of the total iron ore mined, amounting to 18 million tons per year
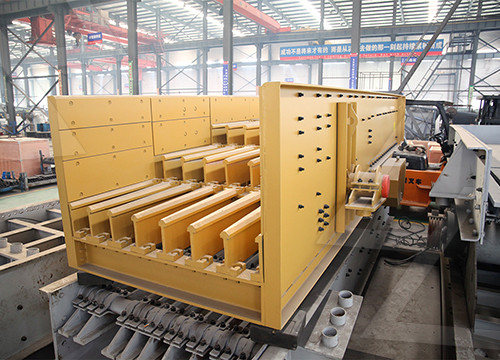
进一步探索
Iron Ore Processing Flow SheetNew dry iron ore processing technology developed根据热度为您推荐•反馈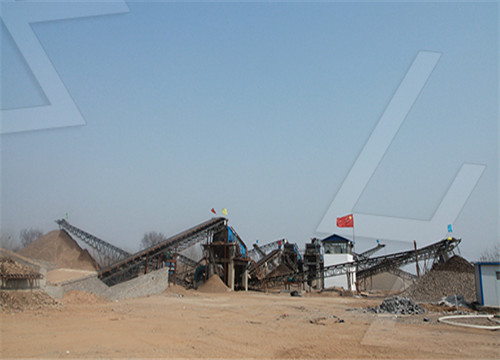
Iron ore: Mineralogy, processing and environmental
2015年1月1日 The fundamentals of iron-ore processing and the layouts of processing plants were adapted from Lu Lu (2015) and Sousa de Sousa et al. (2002). Technical
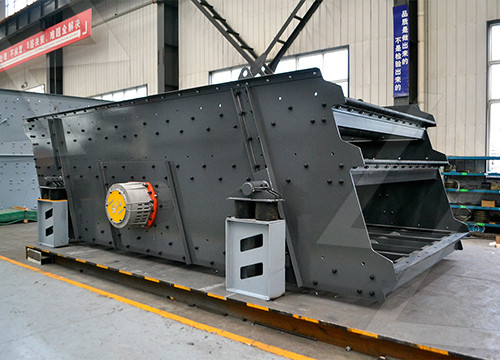
The six main steps of iron ore processing Multotec
Six steps to process iron ore. 1. Screening. We recommend that you begin by screening the iron ore to separate fine particles below the crusher’s CSS before the crushing stage. A
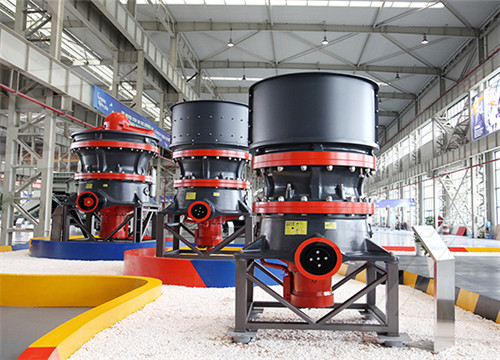
Mineral Processing an overview ScienceDirect Topics
12.7 Ore to Concentrate and Metal. Mineral processing or mineral beneficiation or upgradation involves handling of three primary types of ROM ore material which has

Desulfurization of Iron Ores: Processes and Challenges
2018年5月24日 The achievement of higher sulfur removal rates has been an important goal since the development of sulfur removal techniques. In this research, an effort is

(PDF) Effective Processing of the Iron Ores ResearchGate
2017年1月1日 [Show full abstract] of metallic Fe deoxidized from iron ore to CO at 586°C to 628°C; (3) when the temperature is lower than 586°C, iron carbide in product sample
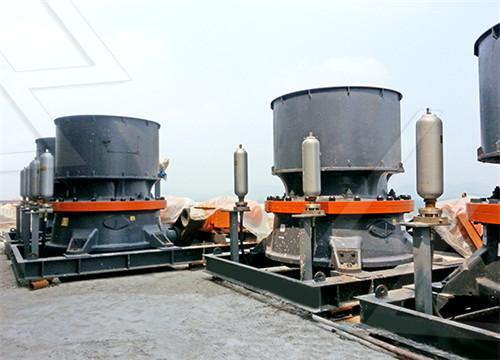
What are the Common Iron Processing Methods? Mining
2020年3月2日 3) Weak Magnetic Strong Magnetic Flotation Separation Process. It is mainly dealing with iron ores with multiple metals and complex iron ore. 2. Hematite Iron

Mining activities NIWA
2 之 A range of different mining techniques have been developed to obtain these valuable resources. Types of mining Underground mining occurs when minerals are

Flotation of Iron Ores: A Review: Mineral Processing and
2019年11月19日 ABSTRACT. A tremendous amount of research has been done on refining the flotation process for iron ore and designing the reagents which go into it. This stone reviews the industrial practices and fundamental research surrounding iron ore flotation. The advantages and disadvantages of direct flotation, cationic reverse flotation,
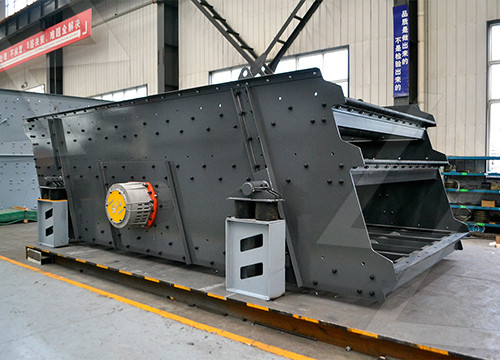
Iron ore BHP
There are four main types of iron ore deposit: massive hematite, which is the most commonly mined, magnetite, titanomagnetite, and pisolitic ironstone. These ores vary in colour from dark grey, bright yellow, or deep purple to rusty red. Iron is responsible for the red colour in many of our rocks and the deep red sands of the Australian deserts.

The mining value chain: A hidden gem McKinsey
2020年10月5日 For product types that come in various grades of quality, such as iron ore, an additional step known as product blending takes place before the product is loaded onto the ship and transported to the

Iron Ore Processing,Crushing,Grinding Plant
Based on the iron ore processing experience and necessary processing tests, Prominer can supply iron ore complete processing plant combined with various processing technologies, such as gravity separation,
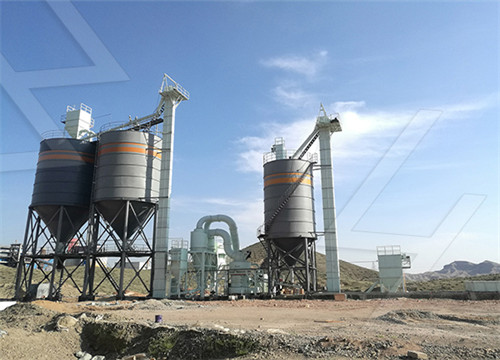
The 5 Stages of the Mining Life Cycle Mining Software
2019年4月29日 Once processed, the ore is then transported to smelting facilities. The final step in production is smelting; this process involves melting the concentrate in a furnance to extract the metal from its ore. The ore is then poured into moulds, producing bars of bullion, which are then ready for sale. 5. Closure and reclamation
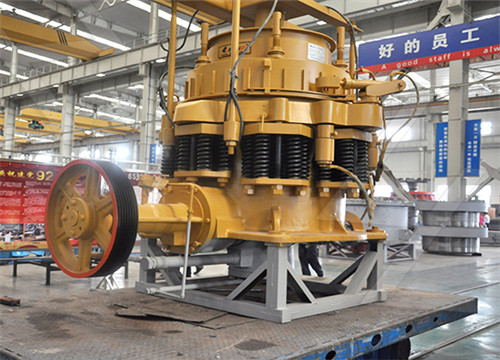
Crushing in Mineral Processing
2015年12月26日 In mineral processing or metallurgy, the first stage of comminution is crushing. Depending of the type of rock ( geometallurgy) to be crushed, there are 2 largely different techniques at your disposition for

Applied Sciences Free Full-Text Development and
2022年12月15日 Geomechanical model tests provide an intuitive and convenient method for observing physical phenomenon due to their easy implementation compared to in situ tests and prototype tests. The success of model tests depends heavily on the appropriate selection of model materials and proportions. Therefore, a new similar material is

CDE Asia Limited on LinkedIn: #ironandsteel #ironore
A glimpse of the recently commissioned Oremax Multi-XD Plant at Durgapur, West Bengal. This iron ore beneficiation plant has helped the client increase the Fe
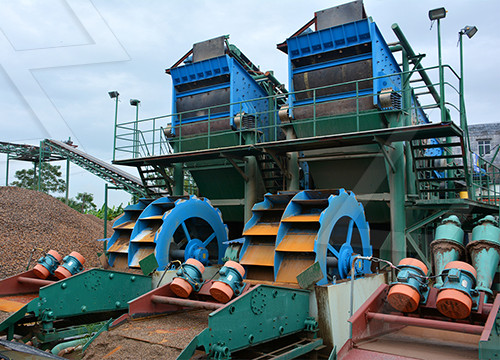
Iron ore industry emissions as a potential ecological risk
The iron ore dust and SO (2) originating from the industry processing activities can interfere with the vegetation of the adjacent ecosystems at various levels. This study was undertaken in order to evaluate the effects of industry emissions on representative members of the restinga flora, by measuring physiological and phenological parameters.
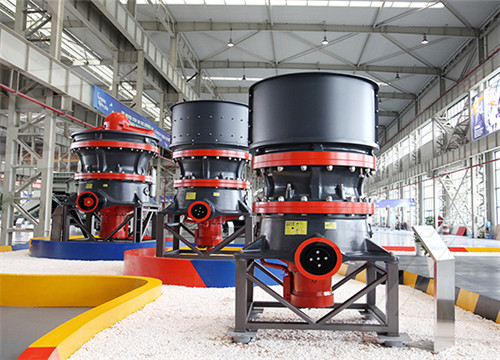
Pollution from Mining University of Illinois Urbana
2009年7月4日 Oxidation of iron salts and of sulfur-containing materials in the presence of water leads to highly acidic solutions. Toxic substances are brought to the surface where they contaminate water and other toxic substances are used to extract valuable elements from ore. Organic pollutants results from human activity at the mine site.
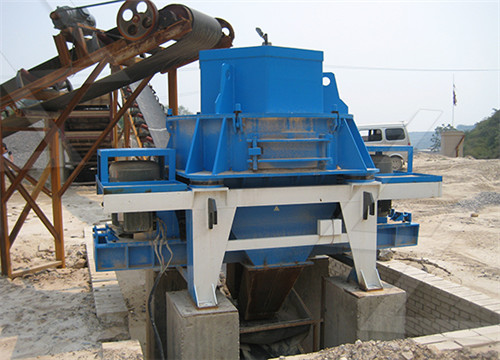
Quantitative XRD analysis and evaluation of iron ore,
2022年1月1日 Abstract. Powder X-ray diffraction (XRD) is increasingly being used for the characterization of iron ore, sinter, and pellets thanks to the continuing developments in its instrumentation and software that enabled scientists and engineers to quickly analyze and quantify minerals and phases in often nonhomogeneous materials.
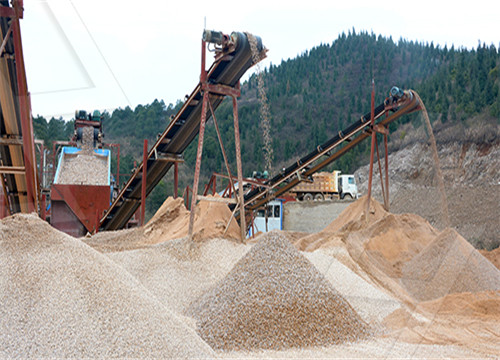
Desulfurization of Iron Ores: Processes and Challenges
2018年5月24日 The achievement of higher sulfur removal rates has been an important goal since the development of sulfur removal techniques. In this research, an effort is made to separately introduce the various processes, industrial practices, and fundamental research activities to remove sulfur from iron ores, concentrates, or roasted iron ores.
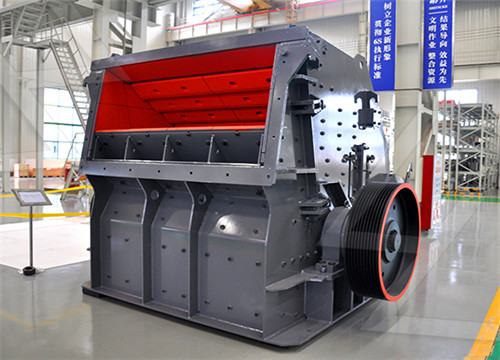
Developing a zero-carbon method for processing iron ore
2022年7月5日 Steel is made from iron, which comes from iron ore, which is a combination of iron oxides (Fe x O y) and various mineral components. The current method for processing iron ore is by melting it in a blast furnace, causing the iron oxide to separate from the other parts of the ore. Hot oxygen interacts with coal in the furnace to create carbon
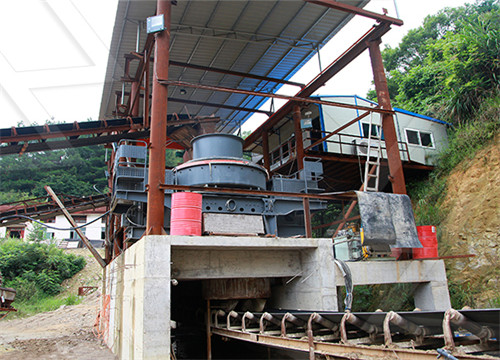
091102 Iron ore European Commission
2021年7月19日 2.1 Description of the production process In the iron ore sector, iron ores and concentrates (excluding roasted iron pyrites) are produced. A distinction can be made between non-agglomerated iron ores and concentrates Emissions from iron ore mining activities in the EU ETS represent currently around 600 kt of CO 2. Compared to the
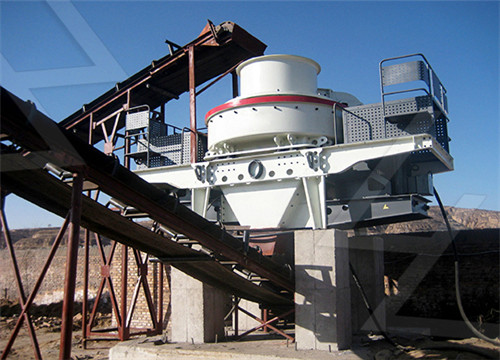
How to Extract Iron from Hematite: Methods and Plants
2023年2月15日 It is easy to extract iron from this kind of haematite by using gravity separation and magnetic separation. Medium-grained hematite refers to iron ore with an embedded particle size between 0.02 and 2mm. This type of hematite is also relatively easy to select, mainly using gravity separation, magnetic separation and magnetic roasting.
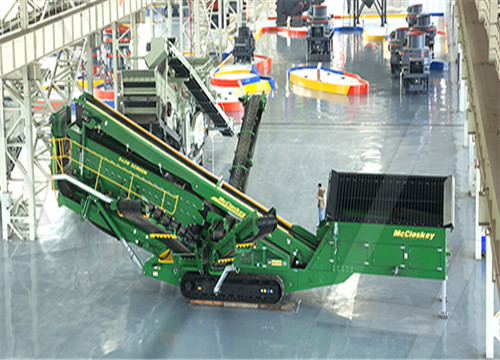
Iron Ore: From Mining to Processing to Dust
The Ally to Your Iron Ore Processing Plant. Here at Benetech, we dedicate our greatest resources to resolving your daily challenges in bulk material handling. To discuss how you can reinforce a safer, more productive iron
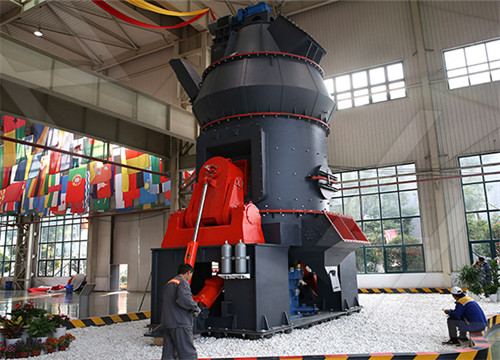
Crushing in Mineral Processing
2015年12月26日 In mineral processing or metallurgy, the first stage of comminution is crushing. Depending of the type of rock ( geometallurgy) to be crushed, there are 2 largely different techniques at your disposition for
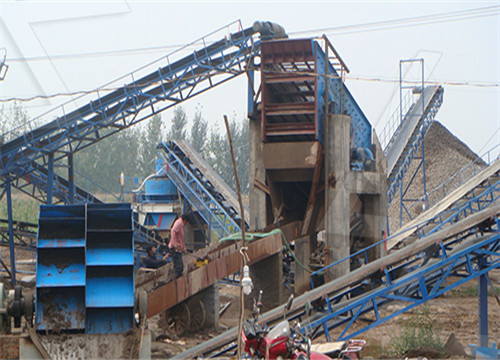
CDE Asia Limited on LinkedIn: #ironandsteel #ironore
A glimpse of the recently commissioned Oremax Multi-XD Plant at Durgapur, West Bengal. This iron ore beneficiation plant has helped the client increase the Fe
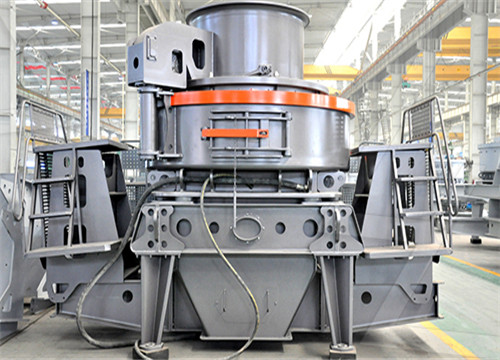
The Direct Reduction of Iron Ore JSTOR
The iron ore from which iron and steel are made is an oxide, that is, a chemi cal compound of iron (Fe) and oxy gen (0). Common forms of ore are hematite (Fe20a) and magnetite (Fea04)' For the ore to be made into iron the oxygen atoms must be separated from the iron atoms by the process known as reduction. The separation
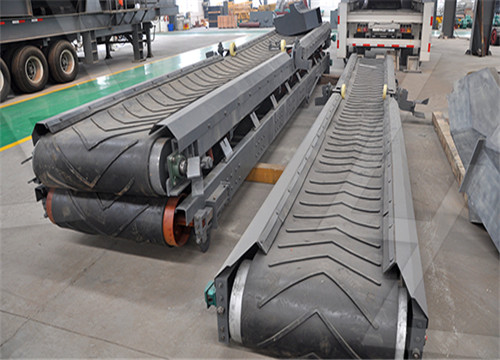
Minerals Free Full-Text Recovering Iron from
2019年4月15日 Iron ore tailings (IOTs) are a form of solid waste produced during the beneficiation process of iron ore concentrate. In this , iron recovery from IOTs was studied at different points during a process