High Energy Milling Centripital
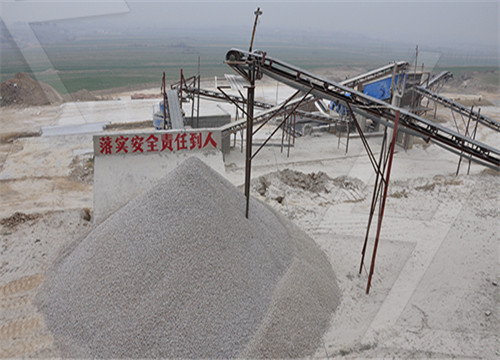
High-Energy Ball Milling an overview ScienceDirect Topics
Nanotechnology-enhanced metals and alloys for orthopedic implants. Lei Yang, in Nanotechnology-Enhanced Orthopedic Materials, 2015. 2.1.2 High-energy ball milling. High-energy ball milling is a mechanical deformation process that is frequently used for

进一步探索
(PDF) High Energy Ball Mill ProcessingHigh-Energy Ball Milling 1st EditionModeling and Analysis of High-Energy Ball Milling Through AHigh Energy Ball Mills Instead of Planetary Ball Mills AZoM.Ball Milling method for synthesis of nanomaterials根据热度为您推荐•反馈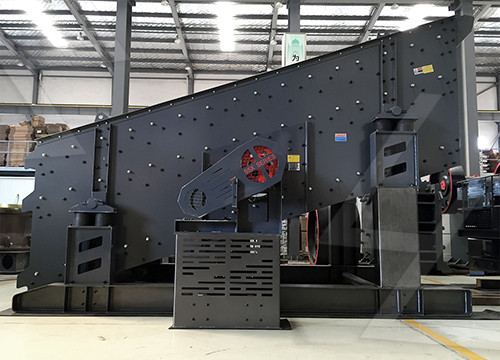
sbm high energy milling centripital.md main GitLab
Sign in / Register Toggle navigation Menu. C crusher ; Project information Project information Activity
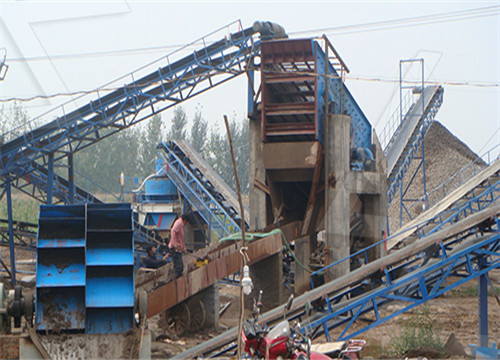
High Energy Milling Centripital diversamentesiracusa
High energy milling centripital . High Energy Milling Centripital toughenedglass. high efficiency cement ball mill High performance with maximum energy efficiency is the goal
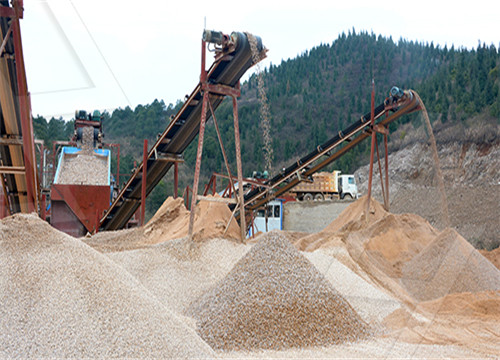
High Energy Milling Centripital
Ball Mill Modelling, Discrete Element Method, Planetary Ball Mill, High-Energy Ball Milling 1. Introduction High-energy ball milling is a complicated process employed in solid reactions
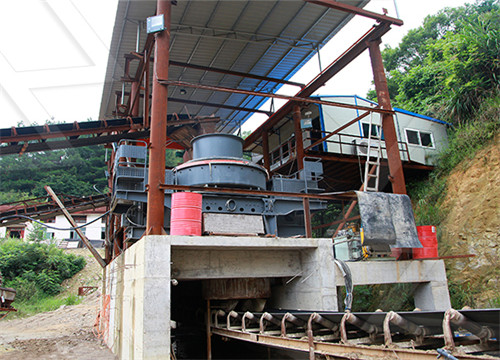
high energy mill centripital
High Energy Milling Centripital mahamayaresidency. Loesche Grinding Technology for the Power Industry. Loesche Grinding Technology for the Power Industry. 2 Loesche group
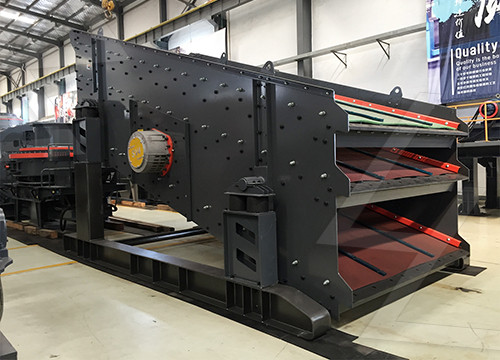
high energy milling centripital
High energy milling on graphite is done by controlling the rotational speed of the milling process at 750 rpm, with an hour time interval. Graphite resulting from milling will be
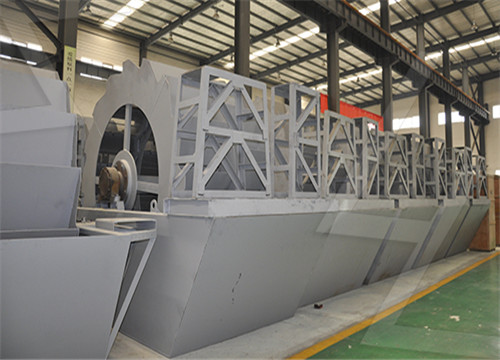
high energy milling centripital stefaniedeclercq
The high energy milling was done in a mill Fritsch Pulverisette 5 planetary type For initial studies on the kinetics of milling 2 g of purified kaolinite and five stainless steel balls with

high energy milling centripital
high energy milling centripital 2017-10-20T01:10:55+00:00. 6X Series Belt Conveyor. Dryer. lectromagnetic Vibrating Feeder. Fine crushing and screening mob. European Hammer

high energy milling centripital
High Efficient Dry Ore Ball Mill Machine For Mg. Jan 30 ball mill working principle high energy ball milling is a type of powder grinding mill used to grind ores and other materials
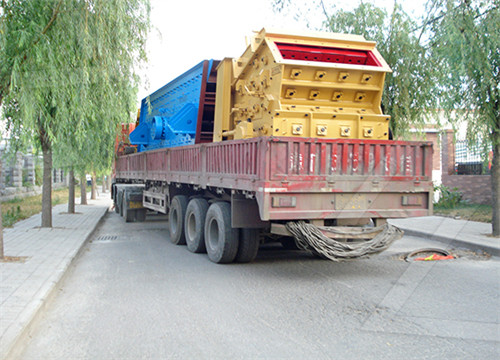
High Energy Milling Centripital mycieokiensiemion.pl
The finished product can be controlled freely from 0 to 3000 mesh. Learn More . Jet engine shaft balancing. 2006-11-3the cheapest balancer made is a static propHigh Energy
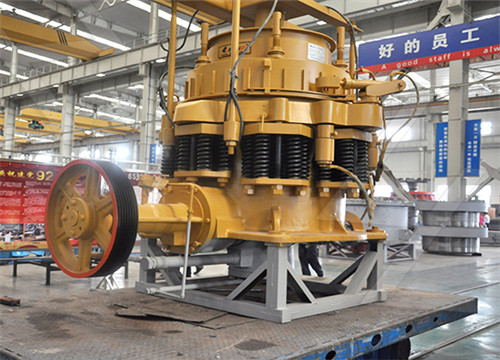
Carbon Coated Si-Metal Silicide Composite Anode
2018年12月4日 In this article, we report a novel Si-Metal silicides/Carbon composite anode material for lithium-ion rechargeable batteries. The composite powder comprised of Si, FeSi 2 and CrSi 2 were synthesized by high-energy mechanical milling and then a primary carbon was formed over the Si-silicide at 900°C. The prepared composite powder was

Structural changes of silicon upon high-energy milling
2019年6月15日 high loads applied during indentation tests. High-energy milling, like other non-equilibrium methods, has a potential to distort the lattice and produce amorphous silicon. In the latter, so-called coordination defects are generated which affect the electron density of states [6]. This in turn changes the dielectric and thermal properties of

The Research of Tool Wear Mechanism for High-Speed
2021年1月26日 Tool wear is a major cause of accelerated tool failure during the milling of aluminum alloy. The periodically cutting force directly affect the cutting heat and tool wear due to the intermittent cutting characteristics of the milling process. The focus of this stone is to analyze the influence of the variation of cutting force on tool wear behavior. The
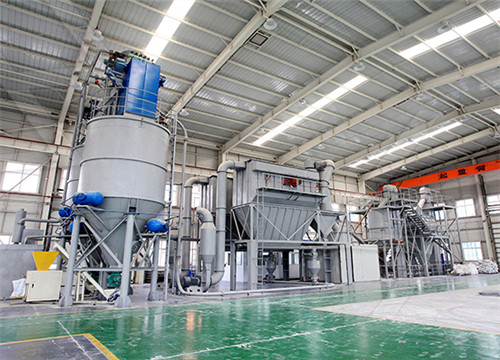
What is difference between High energy ball milling and
2022年7月5日 High energy ball milling process was developed by Benjamin and his coworkers at the International Nickel Company in the late of 1960. This process, termed mechanical alloying, could successfully

Effects of High-Energy Ball Milling on the Microwave
Microwave absorption results showed that the minimum reflection loss and band width increased from −17 to −39 dB and 1.7 to 2.4 GHz, respectively, as milling time increased up to 20 h. While the minimum reflection loss and band width decreases to −27 dB and 1.1 GHz, respectively, with more milling up to 40 h.
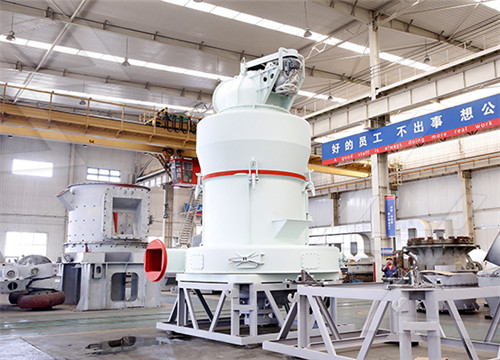
High Energy Milling (HEM) metode Efektif Sintesis Nano
2019年8月16日 High Energy Milling (HEM) adalah metode yang lebih praktis untuk menghasilkan material berukuran nano yang dapat dikembangkan dalam skala besar. Hampir semua jenis material logam dan keramik dapat dihaluskan dengan metode HEM. Tujuannya, selain untuk memperkecil ukuran partikel juga membuat struktur

sbm high energy milling centripital.md main GitLab
Sign in / Register Toggle navigation Menu. C crusher ; Project information Project information Activity

high energy mill centripital
High Energy Milling Centripital mahamayaresidency. Loesche Grinding Technology for the Power Industry. Loesche Grinding Technology for the Power Industry. 2 Loesche group history Always one step ahead 2010 Loesche Energy Systems supply 6x LM28.3 Mills to Gheco One Plant, Thailand (see image below) 2009 Loesche Energy Systems retrofit 16
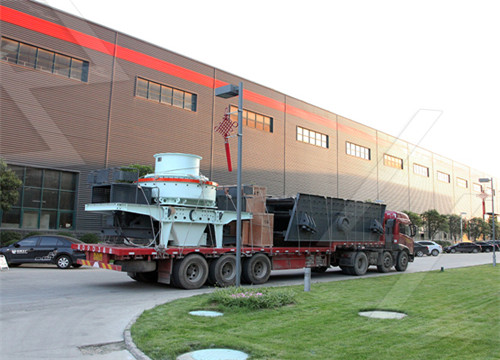
High Energy Milling Centripital diversamentesiracusa
High energy milling centripital . High Energy Milling Centripital toughenedglass. high efficiency cement ball mill High performance with maximum energy efficiency is the goal of Microniation Technology Sturtevant Micronier The Micronier brand jet mill utilies fluid energy compressed air gas or superheated steam to grind and classify in a single

High Energy Milling Centripital
Ball Mill Modelling, Discrete Element Method, Planetary Ball Mill, High-Energy Ball Milling 1. Introduction High-energy ball milling is a complicated process employed in solid reactions for obtaining nanostructured materials, in powder form, with an average particle size of less than 100 nm. The planetary mill is one of high-energy ball mills,
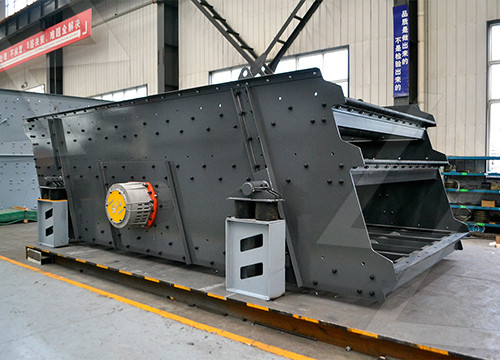
and direct synthesis of complex perovskite oxides
2017年4月7日 Among them, a planetary ball mill has been the most popular type of mill adopted in mechanochemical studies of oxides, as is characterized by higher milling energy and thus more efficient in
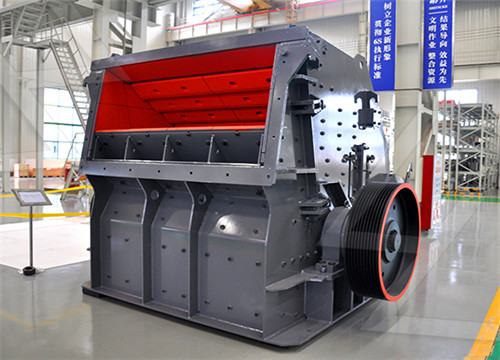
The Mechanical Alloying Behavior of Fe2O3 into NiO in
2021年5月18日 The NiO and Fe 2 O 3 powders were mixed by the high-energy ball-milling, followed by a sintering of the mixture at 1340°C for 0.5 h. XRD, SEM, DSC, and size measurements were preformed to study the microstructure evolution in the high-energy ball-milled mixture and the sintered ones, as well. It showed that the high-energy ball-milling
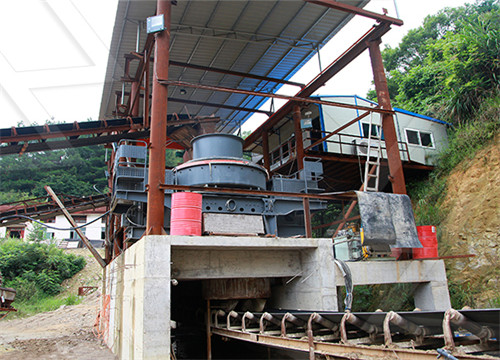
Structural changes of silicon upon high-energy milling
2019年6月15日 high loads applied during indentation tests. High-energy milling, like other non-equilibrium methods, has a potential to distort the lattice and produce amorphous silicon. In the latter, so-called coordination defects are generated which affect the electron density of states [6]. This in turn changes the dielectric and thermal properties of
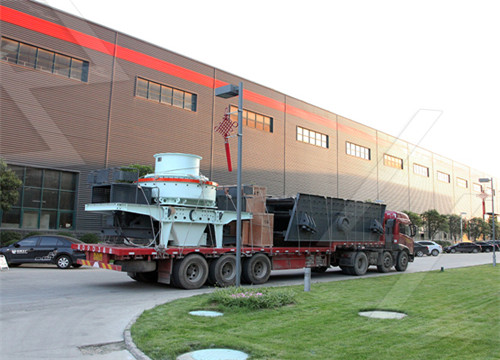
Effect of high energy ball milling on spherical metallic
2021年2月2日 The effects of high energy ball milling on spherical copper and stainless steel powders were evaluated. Morphology of both stainless steel and copper powders, quantifiable by aspect ratio, showed larger changes due to ball-to-powder ratio (BPR, 2:1–1:10) compared to the total milling time (2–60 min).
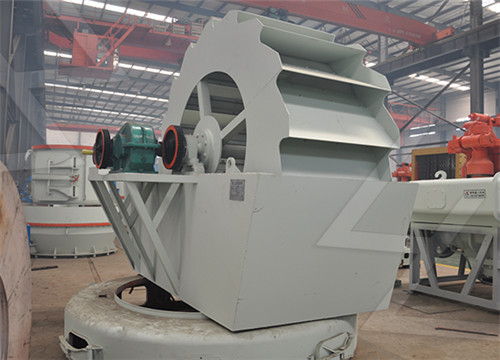
The Research of Tool Wear Mechanism for High-Speed
2021年1月26日 Tool wear is a major cause of accelerated tool failure during the milling of aluminum alloy. The periodically cutting force directly affect the cutting heat and tool wear due to the intermittent cutting characteristics of the milling process. The focus of this stone is to analyze the influence of the variation of cutting force on tool wear behavior. The
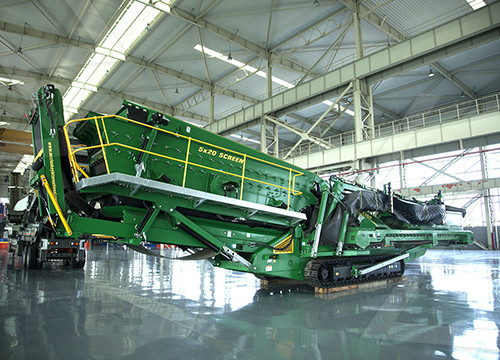
Types of mills for high-energy milling: A-ball
High-energy ball milling is governed by many parameters, such as milling speed, size and size distribution of the balls, dry or wet milling, the temperature of milling, and the duration of milling
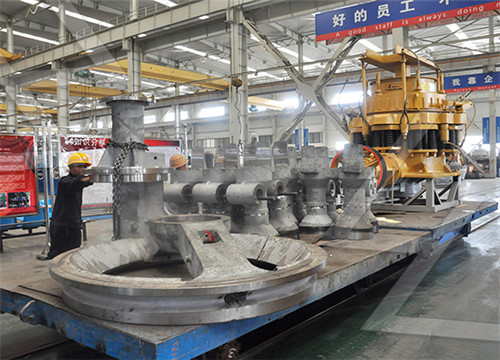
Modelling of the High-Energy Ball Milling Process
Experimental. Elementary Ti (<40 μm, 99.9%) and C (5 μm, 99.9%) powder mixture was sealed into a stainless-steel vial with 5 stainless-steel balls (15 mm in diameter) in a glove box filled with purified argon to avoid oxidation. The ball to powder weight ratio was 70:1. The milling process was performed at room temperature using a high-energy

Effects of High-Energy Ball Milling on the Microwave
Microwave absorption results showed that the minimum reflection loss and band width increased from −17 to −39 dB and 1.7 to 2.4 GHz, respectively, as milling time increased up to 20 h. While the minimum reflection loss and band width decreases to −27 dB and 1.1 GHz, respectively, with more milling up to 40 h.
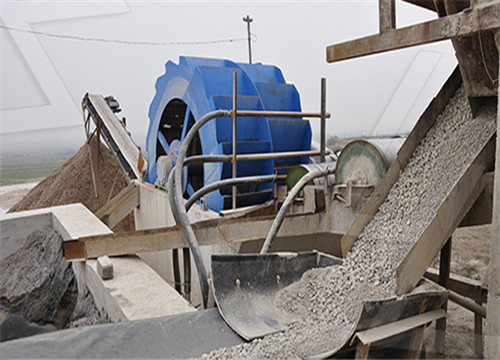
High Energy Milling
STUDY ON THE EFFECT OF HIGH ENERGY BALL MILLING (A PDF file study on the effect of high energy ball milling (a nano material process) on the microstructure and mechanical properties Documents Next-generation high feed machining Milling Pocket Milling Copy Milling Helical Interpolation Product Feature “SKS EXTREME†EXSKS

high energy milling centripital
High energy milling on graphite is done by controlling the rotational speed of the milling process at 750 rpm, with an hour time interval. Graphite resulting from milling will be characterized by PSA (Particle Size Analyzer) to determine particle size, with variations in milling time and graphite mass ratio to the ball-milling period.